The selection of hookah charcoal machines needs to comprehensively consider the characteristics of raw materials, production capacity requirements and budget. Punching machines are suitable for standardized mass production, while extruders are more flexible to adapt to complex shapes. The key is to optimize the formula and equipment parameters (pressure, temperature, moisture content) through experiments, and regularly maintain the core components (molds, screws, hydraulic systems) to ensure product quality and production efficiency.
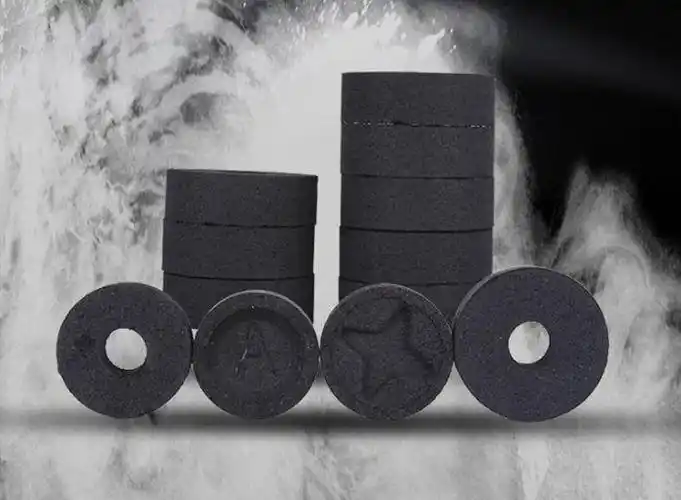
1. Types of hookah charcoal machines
Hookah charcoal production mainly depends on molding equipment, which is divided into the following two categories according to different processes:
Pressing molding machine:
The mixture of charcoal powder and adhesive is pressed into shape (common shapes: round, cubic, hexagonal) by high pressure of the mold and punch.
- Advantages: fast molding speed, suitable for large-scale production.
- Disadvantages: high requirements for raw material particle size, and supporting crushing and screening equipment are required.
Screw extruder:
Similar to the carbon powder extruder, the mixture is extruded into strips through a screw propeller and then cut into the required length.
- Advantages: continuous production, suitable for complex shapes (such as hollow cylinders).
- Disadvantages: high energy consumption, requiring subsequent drying process.
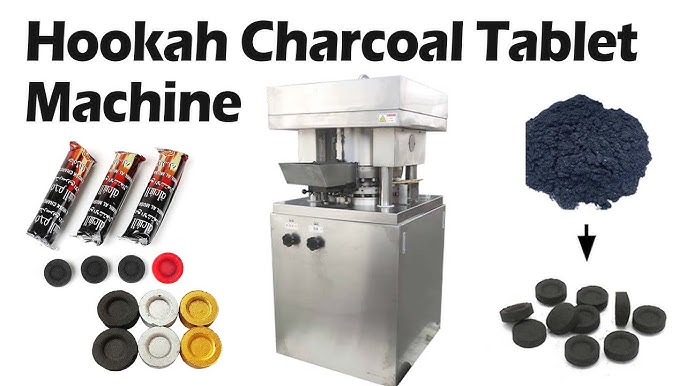
2. Core equipment structure and working principle
(1) Stamping machine
Key components:
- Hydraulic system: provides molding pressure (usually 20-50 tons);
- Mold and punch: hardened steel material, determines the shape of carbon block;
- Feeding system: vibration plate or belt conveys uniform filler;
Workflow:
Mix raw materials → fill mold → high pressure stamping → eject molded carbon block → natural drying or drying.
(2) Screw extruder
Key components:
- Screw propeller: single/double screw design, compressing and extruding raw materials;
- Heating barrel: control temperature (80-120℃) to soften adhesive;
- Cutting device: rotating blade or pneumatic cutter to cut carbon strips.
Workflow:
Mix raw materials → screw extrusion → cutting into sections → drying and curing → surface polishing.
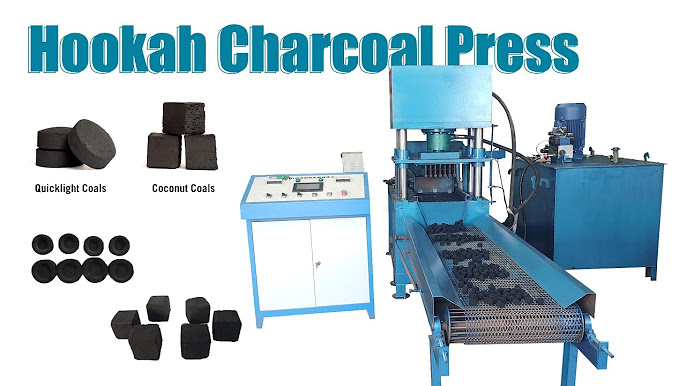
3. Raw materials and formula
Main ingredients:
- Charcoal powder: coconut shell, olive wood and other hardwood charcoal powder (particle size 80-200 mesh);
- Binder: starch, carboxymethyl cellulose (CMC) or natural resin;
- Combustion aid: nitrate (such as potassium nitrate) to adjust the combustion rate.
Typical ratio:
- Charcoal powder: 70-85%;
- Binder: 10-20%;
- Combustion aid: 3-8%.
4. Equipment selection and optimization suggestions
Capacity matching:
- Small equipment: 100-500 kg/day, suitable for home workshops;
- Industrial equipment: 1-5 tons/day, requires matching automated production lines.
Key parameter optimization:
- Pressure control: Insufficient pressure of the punching machine will cause the carbon block to loosen, and too high pressure will easily damage the mold;
- Temperature adjustment: The extruder temperature needs to be dynamically adjusted according to the melting point of the adhesive;
- Mold design: Add exhaust grooves to reduce bubbles, and polish the surface to improve the smoothness of the carbon block.
Energy-saving design:
- Waste heat recovery system: use the exhaust gas from the drying furnace to preheat the raw materials;
- Variable frequency motor: adjust the speed of the screw extruder according to the load.
Tell us about your business and we will provide you with the most professional advice